Presentation of MFX, the new team of Loria
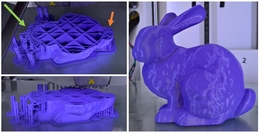
MFX (Matter from Graphics), is the name of the brand new team at Loria. Its field of research? 3D modelling of parts for additive manufacturing, combined with reflection on how to design and produce the objects. Interview with Sylvain Lefebvre, Inria research director and head of the team.
Additive manufacturing: what is it?
Additive manufacturing covers computer-assisted manufacturing processes that gradually add matter to form an object. One of these processes is what we commonly call 3D modelling.
There are numerous reasons behind the appeal of these technologies, which emerged in the mid-1980s.
Initially used for prototyping in industry, they are in the process of revolutionising the way in which engineering invents and manufactures parts. For example, they offer the possibility of directly producing parts in short runs, without any mould or intermediary model: the digital model just needs to be sent to the machine, which will produce it immediately.
These technologies are also attractive for the manufacturing of unique and customised parts, such as made-to-measure prostheses in the medical sector. They also offer a great complexity of shapes, at no additional cost. These manufacturing techniques are thus very promising for reducing the weight of parts in the aerospace sector. They can however also serve as learning tools for understanding shapes and mechanisms, training, and physical visualisation and understanding of shapes and their interactions.
What does the MFX team do, from a scientific perspective?
The members of the team are seeking to model parts for additive manufacturing, and more specifically complex parts – more difficult to create even with a computer, because they are very detailed and must, at the same time, meet tough constraints (thickness, angles, rigidity, total weight). Creating very complex parts subsequently offers the unique possibility of producing – along a same object – behavioural modifications, via a precise structuring of the matter. For example, it becomes possible to vary rigidity, flexibility, porosity, density, colour, etc., in different ways and in different places. And to enable those in charge of design and engineering to design complex parts themselves, the team is looking to automate the modelling methods. For this, it uses synthesismethods: algorithms that will generate the details of the shapes and content, taking all of the constraints into account and, first and foremost, the designer’s objectives.
Of course, the way in which the parts are prepared, i.e. the digital processing that enables the transition from 3D to the manufactured part, is also of great importance. This is what makes it possible to ensure and improve the quality and properties of the parts; all thanks to algorithms which best prepare the instructions carried out by the manufacturing machines.
We have set ourselves a certain number of scientific challenges. We want to represent shapes of a very high complexity, similar to foam and sponges, but whose parameters are all controlled in order to obtain a specific behaviour. We also want to model the geometric constraints of the processes so that they can be taken into account by design and part-processing algorithms. We also manage geometric complexity at all stages: modelling, preparatory calculations and manufacturing, as well as take into account the properties of the materials in the algorithms that guide the processes. Finally, we will need to create new 3D modelling tools to enable medical practitioners, tradespersons and ‘makers’ to use additive manufacturing; in other words, create the fundamental tools behind the interfaces, themselves created by experts in human-computer interaction.
For this, the team has invested in several 3D printers (filament, resin and powder-based), and relies on an international network of academic as well as industry collaborators. On a practical level, the entire team uses the free IceSL software which it is developing for its research and which brings together all of the latest techniques developed by the team.
What are the challenges of the team’s work?
Today, 3D machines can do many things; however, we lack software and methods to exploit all of the possibilities, and in particular how to form objects of high geometric complexity. The algorithms we create must help to manage this complexity and make it possible to use the full potential of additive manufacturing.
Even though there are many potential applications, our team is primarily concentrating, through various collaborations, on applications in the fields of health, design and aerospace.
There are multiple challenges in the medical world: combining different materials on a single part, the manufacture on demand of prostheses or ortheses adapted to the patients’ requirements or which need to change depending on the pathology.
In the aerospace sector, there is considerable potential: making parts lighter, manufacturing parts with new properties (heat exchangers, fluids circulating in porous parts), reductions in stocks and maintenance times in the aviation industry (replacement parts).
The MFX team has only just been created, and it already has some great successes under its belt! Collaborations with prestigious universities (Hong Kong, TU Berlin, TU Delft, the National Research Council (CNR) in Italy), joint projects with scientists specialised in materials (Jean Lamour Institute, Reaction and Process Engineering Laboratory (LRGP)), but also ongoing French National Research Agency (ANR) projects and, already in 2018, four papers accepted in two of the major conferences in the field: ACM SIGGRAPH and I3D, as well as a book which was published in June.
A new team which is already very active – we can only wish it a long and happy life!
Post written by Véronique Poirel, Inria